Experiment and model-based investigation of comminution in a hammer mill
Price
Free (open access)
Volume
Volume 2 (2014), Issue 4
Pages
11
Page Range
362 - 373
Paper DOI
10.2495/CMEM-V2-N4-362-373
Copyright
WIT Press
Author(s)
S. NAIK, Y. FENG & B. CHAUDHURI
Abstract
Particle size reduction of dry granular material by mechanical means, also known as milling or comminution, is undoubtedly a very important unit operation in pharmaceutical, agricultural, food, mineral and paper industries. As comminution is a stochastic and a nonlinear process, an attempt was made to understand this complicated process by conducting parametric studies experimentally and computationally using discrete element method (DEM). Greater size reduction was observed at higher rotational speed of the hammer owing to the greater centrifugal force experienced by the particles. Increase in impeller wall tolerance resulted in rolling mode regime of powder bed, which was found to be significant at low impeller speeds. A numerical model based on DEM was used to simulate a hammer mill and study the breakage and kinematics of the particle motion within the hammer mill. In the simulations, increase in hammer tip speed causes higher frequency of impact of particles per unit time and higher specific energy of impact resulting in generation of much finer end product. A limit can be conceived during the breakage event. This is because as size reduction occurs, the breakage rates can fall for very fine particles as crack propagation ceases. This is because as size decreases the probability of finding a flaw also decreases. Simulations also showed a higher milling rate for big hammers as larger hammers decrease the tolerance between the milling chamber and rotating impeller. To study the effect of material properties, the energy of fragmentation was estimated and it was found to increase as the material became more cohesive.
Keywords
DEM, fragmentation, mill, pharmaceutical
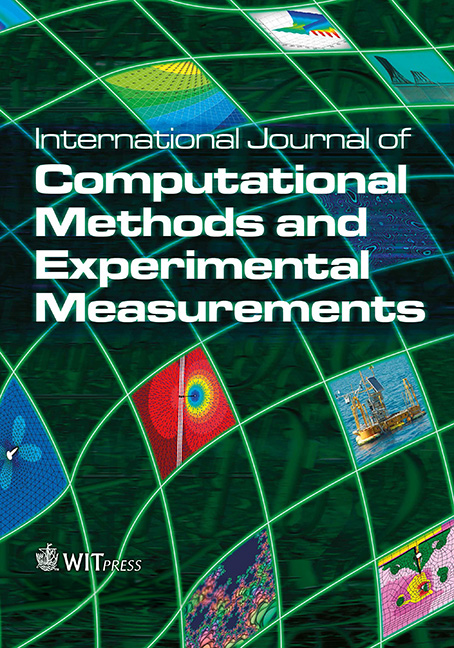