The mechanical and microstructural study of welded AA7075 using different filler metals
Price
Free (open access)
Volume
Volume 5 (2017), Issue 5
Pages
16
Page Range
696 - 712
Paper DOI
10.2495/CMEM-V5-N5-696-712
Copyright
WIT Press
Author(s)
M. ISHAK, M.N.M. SALLEH & S.R. AISHA
Abstract
This paper discussed about the consequences of using different filler metal by metal inert gas (MIG) welding process on aluminium alloys Al 7075 sheet metal joint. Nowadays, Al 7075 is widely used in automobile and aviation industry due to its light weight, strong, and high hardness. Fusion welding, such as MIG and TIG were commonly used in joining the aluminium alloys due to its low cost. However, defects usually occurred using fusion welding because of the inaccurate welding parameters and types of filler metal used. The purpose of this study is to determine whether the filler metal with different elements and welding parameters affect the mechanical properties of welded Al 7075. Welding parameters used were current, voltage, welding speed, and Argon (Ar) as shielding gas. Two different types of filler metal were used which is Electrode Rod (ER) 4043 and ER5356 which is from Al-Si and Al-Mg based element, respectively. From microstructure analysis, fusion zone (FZ) of sample welded with ER4043 has a smaller grain size than that of with ER5356. Both filler produced equiaxed den- dritic grain at FZ. Both samples welded with ER4043 and ER5356 has lower hardness value than heat affected zone (HAZ) and base metal (BM) due to the differences in their elements where ER4043 from Al-Si and ER5356 from Al-Mg group. The weld efficiency of sample welded using ER5356 was 61% which was higher compared to sample welded using ER4043 which at 43% and both sample was brittle fractured. Sample welded with ER5356 was fractured at HAZ due to porosity while sample welded with ER4043 fractured at FZ due to the oxide inclusion.
Keywords
Al 7075, ER4043, ER5356, mechanical properties, microstructure analysis MIG.
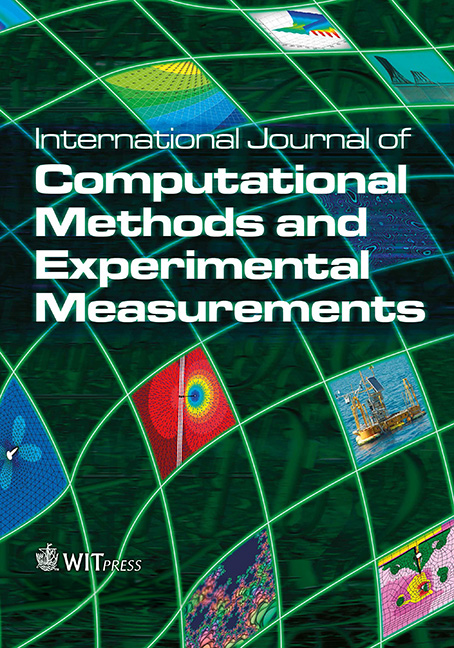