Development of a computational fluid dynamics simulation tool for lubrication studies on cycloidal gear sets
Price
Free (open access)
Volume
Volume 8 (2020), Issue 3
Pages
12
Page Range
220 - 232
Paper DOI
10.2495/CMEM-V8-N3-220-232
Copyright
WIT Press
Author(s)
F. Concli, L. Maccioni & C. Gorla
Abstract
In the last decades, the growing mechatronic sector has promoted the development of more and more compact and efficient gearboxes. The margins of improvement are still big even if, sometimes, finding the optimal solutions is a trial and error procedure. For this reason, the development of dedicated tools for the optimization of the geometry and configuration of gearboxes can significantly increase the development effectiveness and help in reducing design costs. Moreover, having a more efficient solution could also reduce thermal problems during operation and increase the system reliability.
The so-called ‘thermal limit’, i.e. the maximum transmittable power without an overheating of the systems, is particularly critical for high power density and compact solutions. Those relies mainly on planetary, harmonic and cycloidal architectures. While many empirical or analytical prediction models can be found in literature for the prediction of the power losses associated with the gear meshing and the bearing, few reliable models are nowadays available for the losses associated with the interaction with the lubricant, i.e. hydraulic losses. Experimental and computational fluid dynamics studies on parallel axis as well as planetary gear sets have been presented in the past.
The goal of this research is the extension of the applicability range of those numerical approached to cycloidal kinematics for which no studies at all are available with respect to the hydraulic losses.
The main challenge in numerically simulate the lubricant splashing in a cycloidal reduced is related to the topological modification of the computational domain during operation. For this purpose, a specific mesh handling technique, based on a 2.5D mesh, capable to handle the variations of the geometry of the domain was developed in the OpenFOAM® environment. The capability to analytically control the mesh generation at each time step ensures a very high numerical stability and a very high computational efficiency of the solution.
Eventually, the approach was systematically applied to a real geometry and the results compared with those obtained for other gear architectures with comparable performances in terms of dimensions and reduction ratios.
Keywords
CFD, cycloidal gear, efficiency, lubrication, multiphase, power losses.
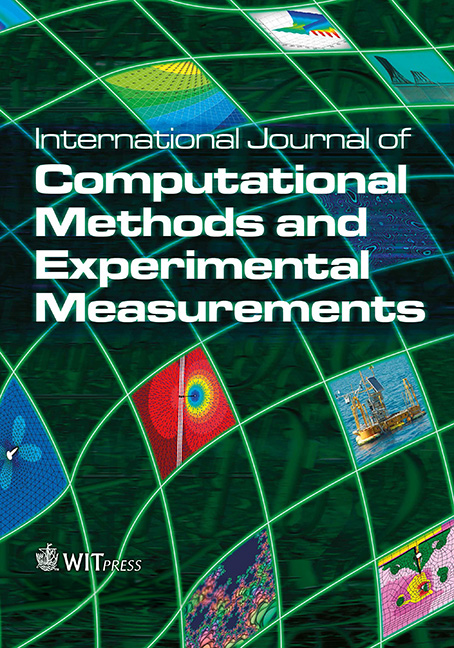