Numerical and experimental analysis of turbulent fluid flow around latest generation cycling frame
Price
Free (open access)
Volume
Volume 8 (2020), Issue 4
Pages
11
Page Range
355 - 366
Paper DOI
10.2495/CMEM-V8-N4-355-366
Copyright
WIT Press
Author(s)
M. Castellini, M. Barbanera, M. Scungio & F. Arpino
Abstract
Computational fluid dynamics (CFD) is a branch of fluid mechanics that uses numerical analysis and data structures to analyse and solve problems that involve fluid flows. Today, CFD plays a decisive role in the cycling industry, which affects not only bicycle manufacturers, but also, above all, bicycle component suppliers. In fact, aerodynamic research takes place not only in the cyclist’s best riding position, but also in the design of the components and frames that make up a racing bike. The frame design is essential both for its ability to oppose the aerodynamic resistance and to adapt the cyclist to the best geometry. Among the multiple outlets of the method, the simulation of external aerodynamic flows shows a fundamental importance for the understanding of the role played by the design of the bicycle. Once a numerical analysis was set correctly, it was then possible to predict with good reliability the fluid dynamic behaviour of an entire structure without the need to use experimental approaches every time. The main aim of this study consists of the validation of a numerical model through experiments conducted on a scale model of a latest generation cycling frame in an open chamber wind tunnel by means of the Particle Image Velocimetry (PIV) technique. In particular, the scale model used was investigated in two specific regions. The experimental data were compared to numerical results obtained employing turbulence model, and the validated numerical tool was subsequently applied to estimate the drag coefficient of two different types of handlebars (aerodynamic and standard versions). The standard cylindrical handlebar folds were replaced by products made of composite and with the most innovative and modern shapes, able to significantly reduce the aerodynamic resistance values. Indeed, in the design phase, the measurement of the drag coefficient is a fundamental procedure. As expected, the presence of aerodynamic profiles generated a low drag coefficient, one of the most important aerodynamic conditions.
Keywords
computational fluid dynamics, cycling frame, drag coefficient, turbulence model, Particle Image Velocimetry.
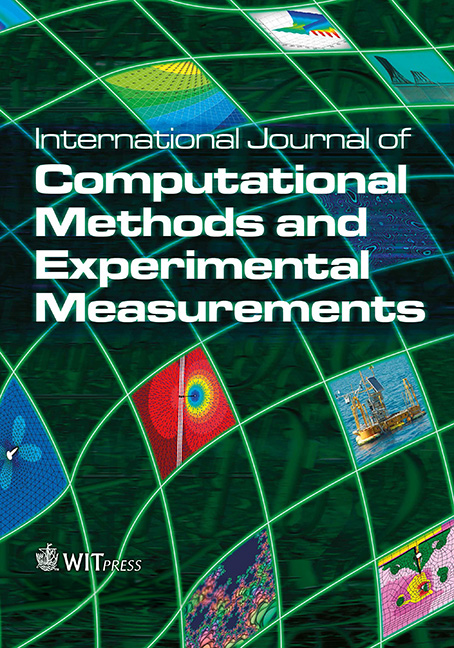